Historic Nuclear Accident Caused by Level Sensor Malfunction in the US
By:Admin
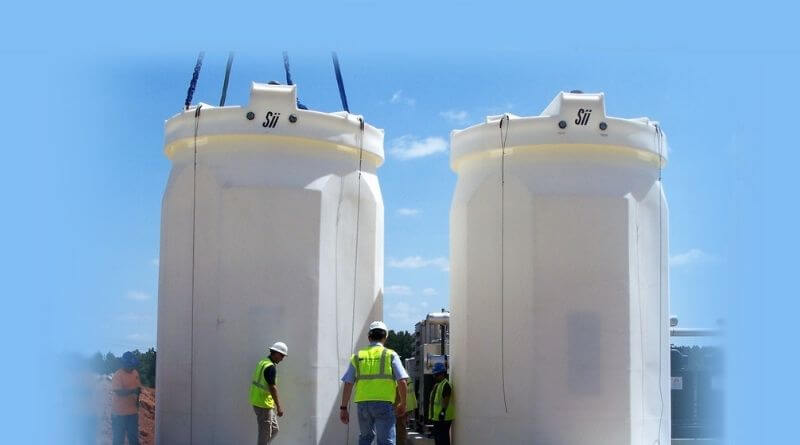
On March 28, 1979, the Three Mile Island nuclear power plant located in Pennsylvania, USA, witnessed a catastrophic event that is still remembered as the worst nuclear power plant disaster in the history of the country. On the 42nd anniversary of the disaster, it is worth revisiting the events that unfolded on that fateful day.
The TMI-2 reactor at the power plant suffered a partial core meltdown that resulted in the destruction of the reactor. The meltdown was triggered by a small malfunction in the secondary cooling circuit that allowed the temperature in the primary coolant to rise. This caused the reactor to shut down automatically.
The situation worsened because the level controls turned off the coolant to the reactor when they detected the presence of cooling water near the top of the tank. The water at the top was not because of the tank being completely filled, but because the water was too little in the tank that it got boiled and swelled up to the top of the tank.
The accident led to the release of radioactive gases and iodine-131 into the atmosphere, which resulted in the evacuation of nearly 140,000 people. Although no fatalities were reported due to the accident, it is estimated that the disaster caused more than $1 billion worth of damage.
The primary cause of the accident was attributed to human error. The failure of the operators to recognize the anomaly in the cooling system led to a delay in shutting down the reactor, which compounded the situation further.
The disaster had a major impact on the nuclear power industry in the United States. It resulted in stricter regulations and safety measures, which significantly affected the development of new nuclear power plants in the country. It also led to a shift towards alternative sources of energy, such as solar and wind power.
The company that operated the TMI-2 reactor, (need remove brand name), also underwent significant changes. The disaster led to the dismantling of its nuclear power division and a focus on other areas of business.
In the years following the disaster, efforts were made to address the environmental and health impacts of the accident. The cleanup of the site took nearly 14 years to complete, and the effects of the radiation exposure on the local population are still being studied.
The Three Mile Island disaster remains a stark reminder of the potential risks associated with nuclear power. While significant progress has been made in improving safety measures and regulations, the risk of accidents cannot be completely eliminated.
As we mark the 42nd anniversary of the disaster, it is important to remember the lessons learned from the tragedy and to continue to strive for safer and cleaner sources of energy for the future.
Company News & Blog
A Guide to Obtaining Concentration Measurements from Common Inline Sensors
The use of common inline sensors is becoming increasingly popular in the industrial sector, particularly in applications where the control of certain components’ concentration is critical. Investment in expensive analytical equipment can place a significant financial burden on companies, but the use of comparatively affordable inline sensors can yield reliable concentration measurements. By utilizing these sensors correctly, companies can effectively monitor and regulate the concentration of key components in real-time, ensuring they meet desired specifications.Inline sensors are typically placed in the process stream to monitor various parameters, including electrical conductivity, ultrasonic waves, refractive index, and more. However, not all inline sensors are suitable for concentration measurement applications. The sensors must measure a physical parameter that directly correlates with the concentration of the component being monitored. In most cases, the physical parameter is directly proportional to the concentration and can be calibrated to provide concentration measurements.To obtain concentration measurements, the sensor must be calibrated, taking into account various characteristics such as flow rate, temperature, and pressure. Calibration is a critical process that requires precision and knowledge of the measuring system’s characteristics to ensure accurate and repeatable measurements. Companies must validate and verify the calibration process periodically to maintain measurement accuracy and quality.The calibration process involves creating a calibration curve that relates the physical parameter measurement to the concentration of the component being monitored. The calibration curve is then utilized by the sensor to calculate the concentration of the component in real-time. Utilizing appropriate sensors, such as the ones offered by the company {}, helps to ensure that the calibration process achieves the required accuracy and repeatability when determining the concentration of the component being monitored.While inline sensors can be used to accurately assess component concentration levels, there are several challenges that companies may face during their use. Companies must take into account the potential impact of the fluid matrix, which may affect the concentration measurements. In some cases, trace impurities or process fluctuations may also affect the accuracy of the inline measurements, necessitating corrective measures.Regular maintenance and calibration checks are essential in ensuring that inline sensors provide reliable measurements. Regular monitoring of the sensors’ performance can help detect drifts in the system and enable companies to maintain and verify the quality of the measurement results promptly. Monitoring also helps ensure that the sensor continues to operate within specification, and any required corrective actions can be taken promptly.It is important to note that inline sensors provide real-time measurements that can aid in process control. Effective monitoring of component concentrations can help companies avoid costly process disruptions, maintain control of their process, and ensure consistent product quality. The use of inline sensors can also help identify and diagnose issues with the process, before any significant consequences arise.In conclusion, inline sensors provide an efficient means of measuring component concentrations in real-time, enabling companies to take corrective action promptly. By utilizing reliable sensors, such as the ones offered by {}, and implementing an appropriate calibration process, companies can effectively monitor and regulate the concentration of key components, enhancing overall process control and product quality. Ongoing monitoring of measurement quality and system performance is critical in ensuring that the sensor continues to operate within specifications and maintains quality control of the process.
How Sensors Monitor Our Bodies and the World Around Us
In recent years, sensors have become an increasingly popular way to monitor our bodies and the world around us. From fitness trackers to smart home devices, these small but powerful devices are changing the way we interact with technology and each other.One of the main benefits of sensors is their ability to collect data in real-time. By measuring everything from heart rate and blood pressure to temperature and humidity, sensors provide us with a wealth of information about our bodies and the environment we live in. This data can then be used to improve our health, increase our productivity, and even save lives.Of course, sensors are not a new technology. They have been used in a variety of applications for decades, from automotive and aerospace engineering to agriculture and manufacturing. However, it is only in recent years that sensors have become more accessible and affordable for everyday consumers.One of the most popular uses of sensors is in fitness trackers. These devices are designed to monitor our physical activity and provide us with feedback on how we can improve our fitness levels. They typically include a range of sensors, including accelerometers, gyroscopes, and heart rate monitors, that work together to provide accurate and detailed data on our movements, heart rate, and calorie burn.Another use of sensors is in smart home devices. These devices use sensors to detect movement, temperature, and humidity, allowing them to adjust their settings automatically to suit our preferences and save energy. For example, a smart thermostat can use sensors to detect when we are home or away and adjust the temperature accordingly, while a smart light bulb can use sensors to detect when we enter and leave a room and turn the lights on and off accordingly.But sensors are not just useful for consumer applications. They also have a wide range of applications in industry, healthcare, and environmental monitoring. For example, sensors can be used to monitor machinery in factories and detect when parts are wearing out, allowing for preventative maintenance and reducing downtime. In healthcare, sensors can be used to detect early warning signs of illness and alert medical professionals, allowing for earlier intervention and better outcomes. And in environmental monitoring, sensors can be used to detect air and water pollution levels, allowing for better management of resources and protection of public health.As sensors continue to become more sophisticated and affordable, their applications will only continue to expand. From self-driving cars to smart cities and beyond, sensors have the potential to revolutionize the way we live, work, and interact with the world around us. The only question now is how we will choose to use this technology to our advantage.
New Level Transmitter Technology Eliminates Impulse Lines and Capillary Tubes
In today’s modern process industries, level measurement is an essential part of monitoring and controlling the fluid level of tanks, vessels, and other containers. There are several ways to measure the level of fluid, including ultrasonic, radar, and differential pressure (DP) level transmitters. Among these, DP level transmitters have been widely used and offer excellent accuracy and reliability.In traditional DP level transmitters, impulse lines and capillary tubes were used to transmit the pressure difference between the liquid and the reference pressure to the measuring cell. However, these lines and tubes were prone to clogging, leakage, or freezing, which caused inaccurate measurements and increased maintenance costs.Thanks to technological advancements, DP level transmitters have evolved to overcome the limitations of traditional designs. Modern DP level transmitters do not use impulse lines or capillary tubes, making them easier to install, operate, and maintain. Instead, they use electronic remote seals or direct-mount seals, which eliminate the need for long tubing runs.Electronic remote seals use a digital signal processor (DSP) to convert the pressure signals from the remote seal into a standard output signal. The remote seal can be located up to 328 feet away from the transmitter, allowing it to be installed in harsh or hazardous environments. The signal is transmitted via two-wire technology, eliminating the need for additional wiring and reducing installation costs.Direct-mount seals can be mounted directly on the process connection of the transmitter, eliminating the need for impulse lines or capillary tubes. They are available in a range of materials and designs to meet different process requirements. Direct-mount seals are easy to install, and they do not require additional calibration or adjustment.Capillary level transmitters offer an alternative solution that eliminates the need for impulse lines and capillary tubes. Instead, they use a single capillary tube to connect the process connection to the measuring cell. The capillary tube is filled with a special fluid that transmits the pressure difference to the cell. Capillary level transmitters are accurate and reliable, and they offer excellent stability over a wide range of process temperatures and pressures.In conclusion, DP level transmitters have come a long way since the traditional designs that used impulse lines and capillary tubes. Modern transmitters offer several solutions that eliminate the need for these lines, making them more reliable, accurate, and easy to maintain. Capillary level transmitters offer additional advantages that make them ideal for certain process applications. When selecting a DP level transmitter, it’s important to consider the specific requirements of the process and choose the best solution that meets those needs.
Ultrasonic Vs Pressure Water Level Measurement: Which Method is More Reliable?
article about the benefits of ultrasonic water level measurement over pressure-based measurement.Water Level Measurement: Ultrasonic vs. Pressure-basedAccurately measuring water levels is essential in a variety of applications, such as water treatment facilities, irrigation systems, and flood detection systems. Traditionally, water level measurement has been done using pressure-based sensors, which measure the water pressure at a certain depth. However, ultrasonic sensors are becoming increasingly popular due to their many benefits over pressure-based sensors.One major advantage of ultrasonic sensors is their accuracy. Unlike pressure-based sensors, which can be affected by changes in temperature, ultrasonic sensors measure the time it takes for sound waves to travel from the sensor to the water surface and back. This means that ultrasonic sensors can provide highly accurate measurements regardless of environmental fluctuations.Another benefit of ultrasonic sensors is their versatility. Ultrasonic sensors can be used in a wide range of applications, including open channels, tanks, and wells. They can also measure water levels with high accuracy over long distances, making them ideal for large bodies of water or difficult-to-reach areas.Ultrasonic sensors are also more reliable than pressure-based sensors. Pressure-based sensors are more prone to clogging, which can affect their accuracy. On the other hand, ultrasonic sensors usually only require periodic cleaning to maintain their accuracy.In addition, ultrasonic sensors are more cost-effective over the long term. Pressure-based sensors require regular calibration and maintenance, which can be costly. Ultrasonic sensors, on the other hand, have a longer lifespan and require less maintenance, making them a more cost-effective option in the long run.One company that offers ultrasonic water level measurement solutions is {}. With over {} years of experience in the industry, {} provides a range of ultrasonic sensors that are designed for various applications. Their sensors are highly accurate and reliable, making them ideal for a wide range of industries, including water management, agriculture, and environmental monitoring.In conclusion, ultrasonic sensors offer a range of benefits over pressure-based sensors for water level measurement. They offer greater accuracy, versatility, reliability, and cost-effectiveness, making them an increasingly popular choice for a wide range of applications. If you are in need of water level measurement solutions, consider exploring the benefits of ultrasonic technology and contacting {} for more information.
How to Measure Water Level with an Ultrasonic Sensor Using a Single Board Computer
Water level measurement is a critical aspect in many industries, including agriculture, hydrology, and even household applications. Inaccurate water level measurement can lead to inefficient use of water resources, causing long-term economic and environmental implications. Therefore, precise and reliable measurement of water levels is imperative, and that's where Ultrasonic Sensor comes in.Ultrasonic Sensor is a non-contact distance measurement sensor that uses sound waves to measure distance. It is a popular choice for water level measurement due to its high accuracy, wide range, and immunity to environmental interference. With the use of a Raspberry Pi, connecting an Ultrasonic Sensor for water level measurement is relatively easy and cost-effective.Here, we will guide you through step by step on how to measure water level using an Ultrasonic sensor and a Raspberry Pi.Hardware requirements:- Raspberry Pi board- Ultrasonic Sensor - Breadboard and jumper wires- A power supply for the Raspberry PiStep 1: Setting Up the Raspberry PiBefore proceeding with the connection of the Ultrasonic Sensor, let's make sure that the Raspberry Pi is ready for use. Connect the Raspberry Pi board to a monitor through an HDMI port, download the latest version of Raspbian operating system, and install it on the Raspberry Pi's microSD card. After installing the OS, connect the Raspberry Pi to the internet via Wi-Fi or Ethernet cable.Step 2: Setting Up the Ultrasonic SensorNext, we need to prepare the Ultrasonic Sensor that will be used for water level measurement. Connect the Echo and Trig pins of the Ultrasonic Sensor to the GPIO pins of the Raspberry Pi. The Echo pin should be connected to GPIO pin number 12, and the Trig pin should be connected to GPIO pin number 16.Step 3: Installing Python LibrariesTo write the code for the water level measurement using the Ultrasonic Sensor, we need to install some necessary libraries. Open the terminal on your Raspberry Pi and type the following command to update the Raspberry Pi:```sudo apt-get update```Then, install the following libraries one by one:```sudo apt-get install python-pip``````sudo pip install rpi.gpio```Step 4: Writing the Python CodeAfter installing all the required libraries, we can now write the Python code for the water level measurement using the Ultrasonic Sensor. Open a new file in Python IDE and add the following code:```pythonimport RPi.GPIO as GPIOimport timeGPIO.setmode(GPIO.BCM)TRIG = 16ECHO = 12print("Distance measurement in progress")GPIO.setup(TRIG, GPIO.OUT)GPIO.setup(ECHO, GPIO.IN)GPIO.output(TRIG, False)print("Waiting for sensor to settle")time.sleep(1)GPIO.output(TRIG, True)time.sleep(0.00001)GPIO.output(TRIG, False)while GPIO.input(ECHO) == 0: pulse_start = time.time()while GPIO.input(ECHO) == 1: pulse_end = time.time()pulse_duration = pulse_end - pulse_startdistance = pulse_duration * 17150distance = round(distance, 2)print("Distance:", distance, "cm")GPIO.cleanup()```This code sends a signal to the Trig pin of the Ultrasonic Sensor, which sends out an ultrasonic wave. The wave travels to the surface of the water and bounces back, hitting the Echo pin of the Ultrasonic Sensor. The time it takes for the wave to return is then measured by the Raspberry Pi, and the distance of the water surface from the Ultrasonic Sensor is calculated using the speed of sound.Step 5: Testing the Water Level MeasurementTo test the water level measurement, run the Python code on your Raspberry Pi, and the distance between the Ultrasonic Sensor and the water surface will be displayed on the screen.```python ultrasonic.py```ConclusionWater level measurement is vital for many industries and applications. With the use of an Ultrasonic Sensor and Raspberry Pi, we can accurately and reliably measure the water level, ensuring efficient use of water resources. This technology has endless possibilities and is becoming increasingly popular in various fields. Contact us to learn more about an Ultrasonic Sensor for Water Level Measurement!
Shop Quality Level Measuring Instruments from Top Suppliers in China - Available Now at Discounted Prices!
Level measuring instruments are an essential tool that is used across many industries. They are primarily used to determine the level of liquids or powder-like materials in tanks and silos. The use of these instruments enables manufacturers to keep track of inventory levels, improve production processes, and prevent overflows. There are different types of level measuring instruments, with one of the most popular being radar level instruments.Radar level instruments use radar waves to determine the level of liquids or materials in tanks. They offer many advantages, including accuracy, reliability, and versatility. They are particularly useful in applications where there are materials that are difficult to measure or where there are harsh conditions, such as high temperatures, pressure, and humidity.One of the key advantages of radar level instruments is their accuracy. They provide precise measurements, even in the presence of obstacles, such as nozzles or agitators. Their accuracy is also not affected by changes in the liquid or material properties, such as density or viscosity. Additionally, they can measure levels that are as low as a few millimeters or as high as several meters.Another advantage of radar level instruments is their reliability. Unlike other types of level measuring instruments, such as ultrasonic or capacitive sensors, radar instruments do not require contact with the material being measured. This means that there is no wear and tear on the sensor, reducing the need for maintenance. Additionally, radar instruments are not affected by changes in the environment, such as temperature or humidity.Radar level instruments are also highly versatile. They can be used to measure a wide range of liquid or material types, including corrosive and abrasive substances. Additionally, they can be used in many different applications, from food production to chemical processing. Because they are non-contact and do not require calibration, they are also easy to install and integrate into existing systems.In conclusion, radar level instruments are an important tool for many industries. Their accuracy, reliability, and versatility make them an ideal choice for measuring liquid or material levels in tanks and silos. They are particularly useful in applications where materials are difficult to measure or where there are harsh conditions. If you are in the market for a level measuring instrument, be sure to consider a radar level instrument for its many advantages and benefits.
Latest News and Articles on Flow Meters in Environmental Science and Engineering Magazine
, Water Flow Meter, Digital Flow Meter, Industrial Flow MeterWhen it comes to managing wastewater and other industrial liquids, measuring flow rate accurately is crucial. This is where flow meters come into play. These instruments are used to measure the volume, velocity, and pressure of flowing liquids or gases.There are several types of flow meters available in the market today, including wastewater flow meters, water flow meters, digital flow meters, and industrial flow meters. Each of these types has its own unique features, benefits, and drawbacks.Wastewater Flow Meters:Wastewater flow meters are specially designed to measure the flow rate of wastewater. These meters are typically used in industrial, municipal, and agricultural settings where wastewater treatment and management are critical.One of the main benefits of wastewater flow meters is their ability to accurately measure the flow rate of highly viscous liquids and solids-laden water. They are also designed to withstand harsh environments and corrosive materials commonly found in wastewater applications.Some of the common types of wastewater flow meters include magnetic, ultrasonic, and Doppler flow meters. Magnetic flow meters use a magnetic field to measure the velocity of wastewater, while ultrasonic flow meters use sound waves to measure flow rate. Doppler flow meters measure the frequency shift caused by flowing wastewater particles.Water Flow Meters:Water flow meters are used to measure the volume and flow rate of water in a range of industrial, commercial, and residential applications. These meters are commonly used in municipal water treatment plants, irrigation systems, and HVAC systems.Digital Flow Meters:Digital flow meters are designed to provide accurate and precise measurements of liquid or gas flow rates. These meters use advanced digital technology, including sensors and data processors, to calculate flow volume and velocity.One of the main benefits of digital flow meters is their ability to provide real-time data and display results in digital format. They are also highly customizable and can be tailored to meet specific industry requirements.Industrial Flow Meters:Industrial flow meters are designed to measure and monitor liquid and gas flow rate in various industrial processes and applications. These meters are commonly used in the chemical, oil and gas, and food and beverage industries.Industrial flow meters can be classified into two main categories: mass flow meters and volumetric flow meters. Mass flow meters measure the mass of the fluid passing through the sensor, while volumetric flow meters measure the volume of the fluid.In conclusion, flow meters are essential instruments for measuring and monitoring fluid flow rates in a range of industrial, commercial, and residential applications. Whether it's wastewater flow meters, water flow meters, digital flow meters, or industrial flow meters, choosing the right flow meter for your specific needs can help you achieve more accurate and reliable results.
Top Pressure Transmitter Suppliers and Traders in Delhi, India
In today's world, where technology and automation are an essential part of various industrial and commercial areas, pressure transmitters play a crucial role. These devices are used to measure and monitor the pressure of liquids and gases in different industrial processes, such as chemical and petrochemical, food and beverage, pharmaceuticals, and many more.Pressure transmitters are essential for ensuring the safe operation of industrial processes, as they enable precise monitoring and control of pressure levels. They provide accurate readings of pressure, which allows operators to detect any fluctuations or abnormalities in pressure levels, which can cause damage or even cause accidents. Instronline is one of the leading suppliers, traders, manufacturers, and dealers of Pressure Transmitters in Delhi, India.Pressure Transmitter PriceThe pressure transmitter price varies based on different factors, such as the type of application, accuracy, range, and brand. Instronline provides a wide range of pressure transmitters at competitive prices, with the high-quality standard to ensure their clients get value for their money. Types of Pressure Transmitters· Differential Pressure Transmitter: These transmitters measure the difference between two pressure points and provide accurate readings.· Absolute Pressure Transmitter: These measure pressure relative to zero pressure, and they are mainly used in applications such as weather monitoring.· Gauge Pressure Transmitter: They measure pressure relative to atmospheric pressure.· Sealed Pressure Transmitter: These are used in applications where pressure is measured in a harsh environment, such as in the oil and gas industry.How to Choose a Pressure TransmitterWhen choosing a pressure transmitter, there are various factors to consider. One of the most crucial factors is the pressure range and accuracy needed for the specific application. Instronline provides pressure transmitters in various ranges up to 400 bar, with high accuracy to ensure the client's needs are met. Another important factor to consider is the compatibility of the transmitter with the process media. This is crucial since some liquids or gases can be corrosive or abrasive to the sensor material, which can affect the accuracy of the readings. Instronline provides pressure transmitters with sensors made of different materials, such as stainless steel, titanium, and ceramic, to ensure the compatibility with the process media.Why Choose Instronline for Pressure Transmitter?Instronline is a reliable supplier, manufacturer, and dealer of pressure transmitters in Delhi, India. They offer a wide range of pressure transmitters from reputable brands to ensure quality. Their prices are competitive, and they provide technical support to their clients, ensuring that the pressure transmitter meets their specific requirements.ConclusionIn conclusion, pressure transmitters are essential in various industrial processes, and choosing the right one is crucial for safe and efficient operations. With the help of Instronline, the client can find the suitable pressure transmitter at a reasonable price, customized to their specific needs. Contact Instronline today for the best deals on pressure transmitters.
Improve Your Hydroponic System with a PH and EC Controller
In the increasingly popular field of hydroponic gardening, the PH and EC levels of your plants are crucial to their overall health and growth. That's where the PH & EC Controller ProSystem Aqua comes in - this powerful tool allows you to easily measure and adjust the PH and EC levels in your hydroponic setup, ensuring optimal conditions for your plants to thrive.First, let's talk about what PH and EC actually are. PH is a measure of the acidity or alkalinity of a solution, and can range from 0 to 14. In hydroponics, the ideal PH range for most plants is between 5.5 and 6.5, although some plants may prefer slightly more acidic or alkaline conditions. EC, or electrical conductivity, measures the concentration of minerals and nutrients in a solution. EC can also vary depending on the type of plant and the stage of growth, but generally falls between 0.2 and 3.0 in hydroponic systems.The PH & EC Controller ProSystem Aqua is designed to help you achieve and maintain these optimal levels by automatically adjusting the PH and EC based on your desired settings. The system comes with two probes - one for PH and one for EC - which are placed in the hydroponic solution. The probes are connected to a digital controller that constantly monitors the readings and alerts you if the levels go out of range. If this happens, the controller will activate a dosing pump to add or subtract the necessary solution to bring the levels back into balance.One of the biggest advantages of the PH & EC Controller ProSystem Aqua is its simplicity. Even if you're new to hydroponics, the system is easy to set up and use. Plus, because it's fully automated, you can trust that your plants are always getting the right levels of nutrients without having to constantly monitor and adjust them yourself.Another benefit of the PH & EC Controller ProSystem Aqua is the time and money it can save you in the long run. By ensuring optimal growing conditions, you'll be able to grow healthier, more robust plants that produce higher yields. This means you'll be able to harvest more in less time, leading to greater profits and savings.In conclusion, if you're serious about hydroponic gardening, the PH & EC Controller ProSystem Aqua is a must-have tool for achieving optimal PH and EC levels in your setup. By taking the guesswork out of maintaining your hydroponic solution, this system can lead to healthier plants, higher yields, and greater success in your garden. So why wait? Take your hydroponic gardening to the next level with the PH & EC Controller ProSystem Aqua today!
Top Products of Electromagnetic Flow Meters for Precision Flow Measurements
and Electromagnetic Flow Meter Supplier throughout.Electromagnetic Flow Meter – A Perfect Solution for Accurate Flow MeasurementIn modern industries, handling fluid or gas flow is a crucial part of production, manufacturing, and processing. One of the critical aspects of fluid handling is measuring flow rates accurately and consistently. This is where Electromagnetic Flow Meters come in handy, as they provide a reliable, accurate, and cost-effective solution for flow measurement needs.As a leading Magnetic Flow Meter Factory and Electromagnetic Flow Meter Supplier, we understand how crucial it is to have precise flow measurement, as it impacts the entire production line's efficiency and profitability. Our high-quality Electromagnetic Flow Meter products are designed to cater to various industries' diverse flow measurement needs, from water treatment to petrochemicals.What is Electromagnetic Flow Meter?Electromagnetic Flow Meters, also known as Mag Meters, are devices that measure fluid flow rates using electromagnetic principles. The measurement principle involves inducing a voltage signal in the conductive fluid as it flows through a magnetic field. This voltage generated is proportional to the fluid's velocity and, accurately obtained, provides a reading of the flow rate.Benefits of Using Electromagnetic Flow Meters1. Accurate and Reliable MeasurementsOne of the significant advantages of Electromagnetic Flow Meters is their exceptional accuracy in measuring flow rates. They provide reliable measurements with minimal uncertainty, even in challenging fluid conditions, such as slurries, dirty fluids, and high temperatures.2. No Moving PartsElectromagnetic Flow Meters have no mechanical moving parts, making them low maintenance devices. This eliminates the need for frequent repairs, minimizing downtime and maintenance costs. Additionally, this makes them more durable and dependable for long term usage.3. Easy to Install and UseElectromagnetic Flow Meters are easy to install, and their low-profile design is space-saving, making them suitable for various industrial applications. They require little to no calibration, and their readings are straightforward to interpret, making them user-friendly for various applications.4. Wide Range of ApplicationsElectromagnetic Flow Meters are versatile devices that can measure a broad range of fluids, including corrosive and abrasive ones. This ability makes them suitable for various industrial applications, including water treatment plants, petrochemicals, food and beverage, pharmaceuticals, and more.In summary, Electromagnetic Flow Meters are reliable, accurate, and cost-effective flow measurement devices that cater to various industries' needs. At our Magnetic Flow Meter Factory and Electromagnetic Flow Meter Supplier, we pride ourselves on providing high-quality products and exceptional customer service to our clients. Our commitment to innovation and technology ensures that we stay at the cutting edge of the industry, providing our clients with the best-in-class products for their flow measurement needs.